Actualizado a: 16 de abril de 2024
Si sientes curiosidad por saber qué es una foundry y su funcionamiento, para tratar de comprender mejor cómo se fabrican los chips, aquí tienes una buena guía para comenzar a comprender estas infraestructuras tan avanzadas.
También te interesará conocer:
- Chip binning: qué es
- Engineering sample: qué es este chip
Modelo IDM

El modelo IDM (Integrated Device Manufacturer, por sus siglas en inglés) es un modelo de negocio en la industria de semiconductores que implica que una empresa es responsable tanto del diseño del chip como de su fabricación.
En este modelo, una empresa tiene el control total del proceso de diseño, fabricación y comercialización de sus productos. Esto le permite a la empresa tener un mayor control sobre la calidad del producto, la entrega y el costo. Además, la empresa también puede desarrollar soluciones personalizadas para satisfacer las necesidades específicas de sus clientes.
Históricamente, el modelo IDM fue la forma en que se llevaba a cabo la mayoría de la fabricación de semiconductores, con empresas como Intel, AMD, Texas Instruments, Samsung, IBM, y Motorola que controlaban todo el proceso de diseño y fabricación de sus productos. Sin embargo, con el aumento de los costos de fabricación y el aumento de la complejidad de los chips, muchas empresas han optado por tercerizar la fabricación a foundries especializadas, en lugar de mantener la producción en casa.
A pesar de esto, algunas empresas todavía siguen utilizando el modelo IDM, y muchas de ellas han sido capaces de mantenerse a la vanguardia en la industria de semiconductores gracias a su capacidad para innovar y desarrollar soluciones personalizadas para sus clientes. Además, algunas empresas han adoptado un modelo híbrido, en el que combinan la fabricación interna con la subcontratación a foundries para maximizar la eficiencia y la flexibilidad.
Cada vez existen menos IDMs puros, y de todos los que había en un inicio, actualmente quedan pocos, como Intel, Texas Instruments, Samsung y poco más. Otras como Motorola, AMD, etc., han pasado a ser fabless, vendiendo sus fábricas. Por ejemplo, las fábricas de Motorola terminaron convirtiéndose en Freescale, y las de AMD en GlobalFoundries…
¿Qué es una fabless?
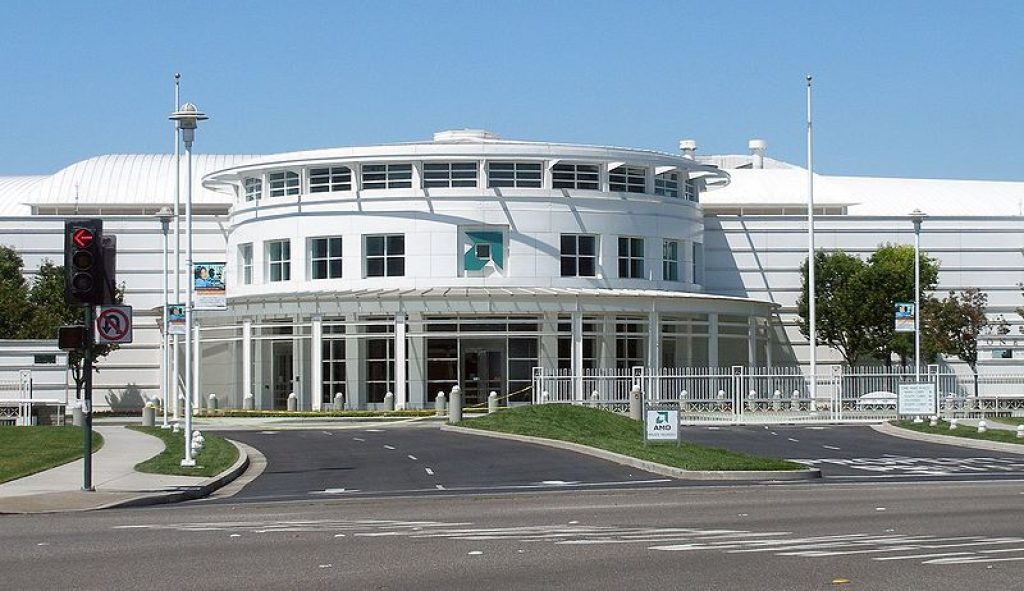
Una empresa fabless (sin fábrica) es una empresa de diseño de semiconductores que se centra exclusivamente en el diseño y desarrollo de chips y subcontrata la fabricación a una foundry (fabricante de semiconductores) especializada en la producción de obleas de silicio y chips.
En otras palabras, una empresa fabless se enfoca en la parte del proceso de producción de semiconductores que involucra la creación del diseño del chip y la validación de su funcionalidad, pero no se involucra en la producción física del chip. En cambio, la fabricación se subcontrata a una foundry que se especializa en la producción a gran escala de chips.
Este modelo de negocio permite a las empresas fabless enfocarse en lo que mejor saben hacer: diseñar chips. Al subcontratar la fabricación, pueden mantener costos bajos y ser más flexibles y rápidos para adaptarse a las necesidades del mercado.
Además, al no tener que preocuparse por la inversión en la construcción, actualización y operación de fábricas de chips costosas y altamente especializadas, las empresas fabless pueden concentrar sus recursos y esfuerzos en la innovación y el desarrollo de nuevos productos, lo que les permite mantener una posición de liderazgo en el mercado de semiconductores.
El modelo fabless ha sido especialmente popular en la industria de los semiconductores, donde la tecnología avanza a una velocidad vertiginosa y las empresas deben mantenerse a la vanguardia en términos de innovación para mantenerse competitivas. Ejemplos de empresas fabless incluyen Qualcomm, AMD, NVIDIA, Broadcom, Motorola, Google, Apple, Mediatek,, entre otras.
¿Qué es una foundry?
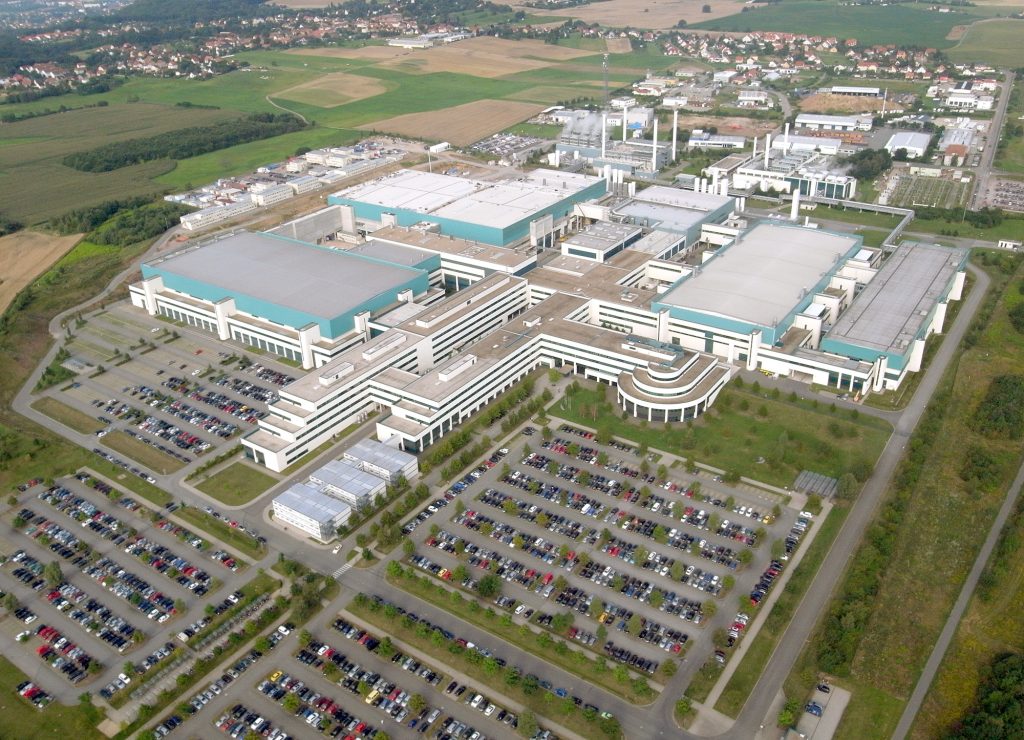
Una foundry, fundición, o fab de semiconductores es una empresa especializada en la producción de semiconductores a gran escala. Foundry es una abreviatura de «fabrication foundry» o «semiconductor foundry».
A diferencia de las empresas de diseño de semiconductores que solo crean diseños de chips y luego subcontratan la producción a una foundry, las empresas de foundry son responsables de todo el proceso de producción de semiconductores, desde la fabricación de obleas de silicio hasta la producción de chips y la realización de pruebas de calidad. Pero no se encargarán ni se involucrarán en el proceso de diseño, aunque haya relaciones entre la fabless y la foundry para optimizar o adaptar los nodos de fabricación en algunos casos.
Las foundries de semiconductores pueden centrarse en fabricar para múltiples clientes, obteniendo buenas ganancias, y permitiendo invertir en actualizar y equipar las caras fabs, sin tener que hacer inversiones en otros campos, como podrían ser las áreas de diseño.
Además de la producción de chips, las foundries también pueden proporcionar servicios adicionales, pruebas y validación de chips, y servicios de fabricación personalizados para clientes de diversos sectores, incluyendo la electrónica de consumo, la industria automotriz, la industria de la comunicación, la industria médica y muchos otros.
Algunas de las principales empresas de foundry de semiconductores incluyen TSMC, GlobalFoundries, Samsung Foundry, SMIC, UMC, entre otras. Estas empresas son líderes en tecnología de fabricación de chips y ofrecen una amplia gama de servicios y soluciones para clientes de todo el mundo. Además, como debes saber, Intel ha puesto en marca recientemente el servicio IFS (Intel Foundry Service), que convierte a la compañía en una especie de IDM 2.0, que no solo diseña y fabrica sus propios chips, sino que también permite prestar servicios de fabricación a terceros o fabless que los necesiten.
No obstante, en la actualidad, Intel no es un IDM puro ni una foundry pura. De hecho, como sabrás, algunos de los chips de Intel, tanto de CPUs, como de GPUs, a lo largo de su historia han sido fabricados por terceros, como puede ser por TSMC.
IDM vs Fabless: ventajas y desventajas de cada uno
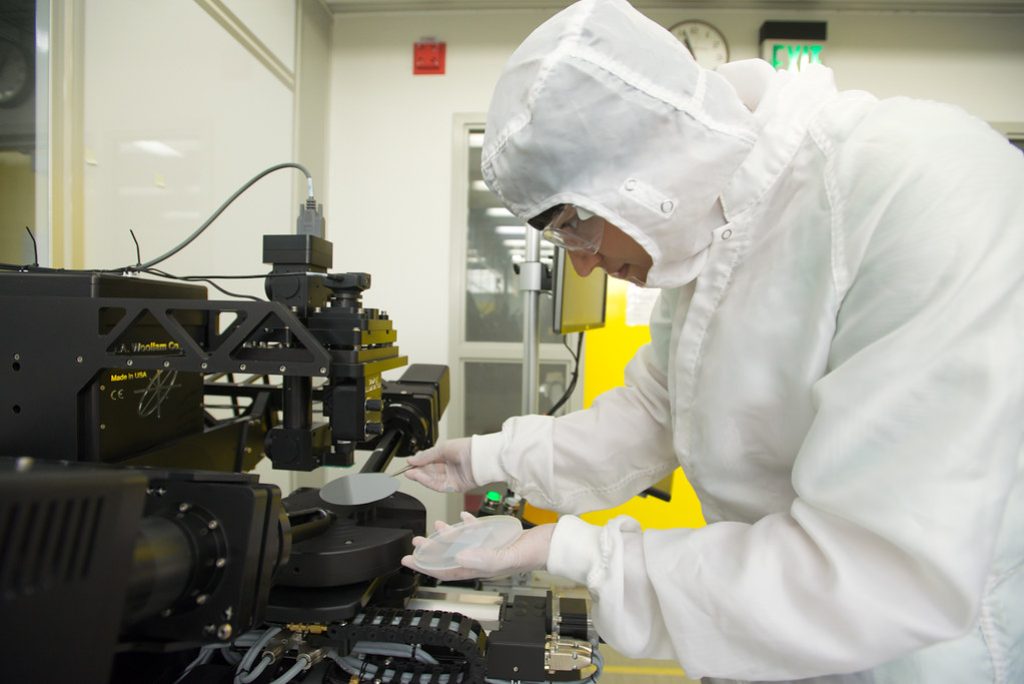
Tanto el modelo IDM (Integrated Device Manufacturer) como el modelo fabless (sin fábrica) tienen sus ventajas y desventajas, y la elección del modelo dependerá de las necesidades específicas de cada empresa y del producto que se esté desarrollando.
Ventajas del modelo IDM:
- Control total del proceso: las empresas IDM tienen el control total del proceso de diseño y fabricación de sus productos, lo que les permite asegurarse de que los productos cumplan con los requisitos de calidad y rendimiento. Además, esto también les permite tener un mayor control sobre el tiempo de entrega y los costos de producción.
- Mayor flexibilidad: al tener la capacidad de controlar todo el proceso de diseño y fabricación, las empresas IDM pueden ser más flexibles y adaptarse mejor a las necesidades del mercado y de los clientes.
- Innovación: al tener todo el proceso de diseño y fabricación en casa, las empresas IDM pueden invertir más recursos en investigación y desarrollo, lo que les permite innovar y lanzar nuevos productos al mercado de manera más rápida.
- Mayores ganancias: el margen de ganacias es mayor, ya que no implica tener que pagar a terceros por la fabricación, que a su vez también queran ganarse un beneficio en la producción.
Desventajas del modelo IDM:
- Altos costos: el modelo IDM requiere una inversión significativa en infraestructura y equipo de fabricación, lo que puede ser prohibitivo para las empresas más pequeñas.
- Menos eficiente: al tener que administrar todo el proceso de diseño y fabricación, las empresas IDM pueden ser menos eficientes y tener mayores costos operativos.
- Limitaciones de capacidad: las empresas IDM están limitadas por su propia capacidad de fabricación, lo que puede limitar su capacidad para responder a la demanda del mercado.
Ventajas del modelo fabless:
- Bajos costos: al subcontratar la fabricación, las empresas fabless pueden evitar los altos costos asociados con la construcción y operación de una fábrica de semiconductores.
- Flexibilidad: al no tener que administrar todo el proceso de diseño y fabricación, las empresas fabless pueden ser más flexibles y adaptarse mejor a las necesidades del mercado.
- Innovación: al no tener que preocuparse por la inversión en la construcción y operación de una fábrica de chips costosa, las empresas fabless pueden concentrar sus recursos y esfuerzos en la innovación y el desarrollo de nuevos productos.
Desventajas del modelo fabless:
- Dependencia de terceros: al subcontratar la fabricación, las empresas fabless pueden depender de terceros para la producción y entrega de sus productos.
- Control limitado de calidad: al no tener el control total del proceso de fabricación, las empresas fabless pueden tener un control limitado sobre la calidad del producto.
- Menor capacidad de producción: al depender de terceros para la fabricación, las empresas fabless pueden tener una capacidad de producción limitada en comparación con las empresas IDM, ya que las foundries generalmente fabrican para otros clientes, y cada uso acuerda una cuota o volumen de wafers u obleas.
- No siempre se tiene acceso al nodo más avanzado: por ejemplo, TSMC reserva el nodo o proceso más avanzado a Apple por un acuerdo entre ambas compañías, mientras que el resto de clientes deben esperar al menos un año a que dicho proceso sea «liberado» y lo puedan emplear.
Como suele ocurrir, tanto el modelo IDM como el modelo fabless tienen ventajas y desventajas, y la elección del modelo dependerá de las necesidades específicas de cada empresa y del producto que se esté desarrollando. Las empresas IDM tienen un mayor control sobre el proceso de fabricación, lo que les permite garantizar la calidad del producto y tener una mayor capacidad de producción, pero también requieren una inversión significativa en infraestructura y equipo. Las empresas fabless pueden ser más eficientes y flexibles, pero tienen un control limitado sobre la calidad del producto y pueden tener una capacidad de producción limitada.
Un poco de historia
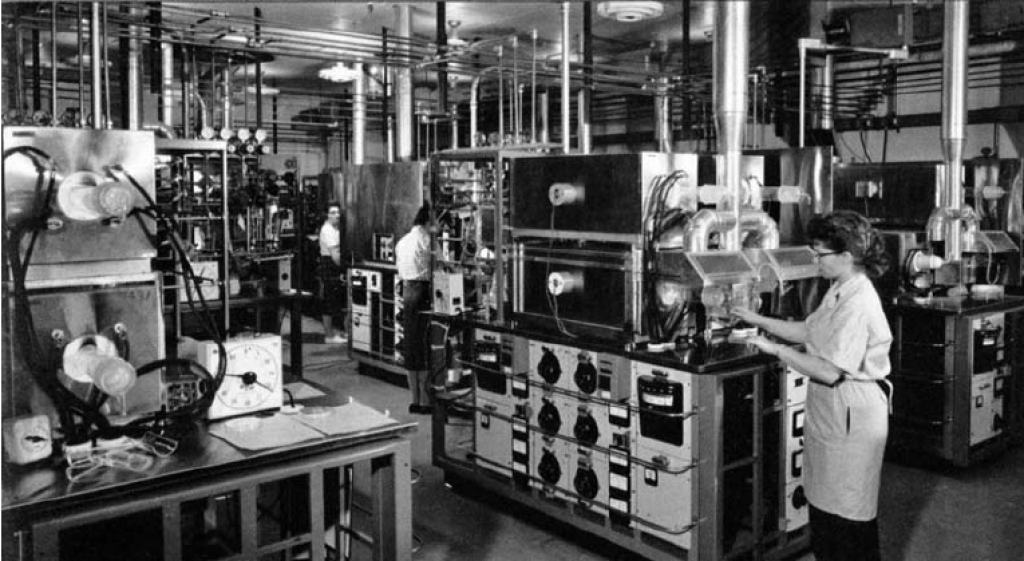
Al principio, no había fábricas especializadas donde se fabricaran obleas de semiconductores. Como tal, la producción era de tamaño limitado y tenía grandes etiquetas de precio. Esta es la razón por la que surgieron las primeras fundiciones, ya que se requería fabricar más y más baratos componentes electrónicos para satisfacer la creciente demanda observada desde las décadas de 1970 y 1980.
En la década de 1980, la mayoría de las empresas de semiconductores poseían y operaban sus propias fundiciones, eran IDMs. Como tal, no había empresas de semiconductores que no fueran propietarias de sus propias fábricas, ya que no tendrían forma de fabricar sus diseños.
El primer cambio en este espacio ocurrió cuando algunas empresas descubrieron que tenían un exceso de capacidad en sus propias fábricas porque una fundición de semiconductores económicamente grande podría resultar más grande que sus propias necesidades para sus propias líneas de productos. En consecuencia, otras empresas pueden tener el problema opuesto: no construyeron una fundición lo suficientemente grande, o la construyeron tarde y tenían más demanda que oferta.
Las empresas de semiconductores comprarían y venderían obleas entre sí para igualar sus necesidades de capacidad. Esto se conoció como el negocio de fundición, análogo a una fundición de acero. De manera similar, las empresas de semiconductores con escasez llevarían sus diseños a otras empresas de semiconductores con capacidad excedente (a menudo incluso competidores) y los fabricarían para ellos.
El siguiente paso en la evolución de la fábrica fue que, a mediados de la década de 1980, algunas empresas se dieron cuenta de que no necesitaban poseer una fábrica para fabricar chips. Estas empresas comprarían obleas de fundición como cualquier otra empresa de semiconductores. Estas empresas llegaron a denominarse, por razones obvias, empresas de semiconductores fabless.
Además, también surgieron algunas foundries puras o servicios de MPW, es decir, empresas que emplearon sus fábricas para producir para terceros. Las primeras para producción en masa, las segundas para producir multitud de proyectos de chips diferentes en un mismo wafer, para encargos más pequeños.
Actualmente, como he mencionado antes, los modelos entre las IDMs puras y las foundries puras está algo borroso, con modelos mixtos como he citado antes.
¿Qué es una sala blanca?
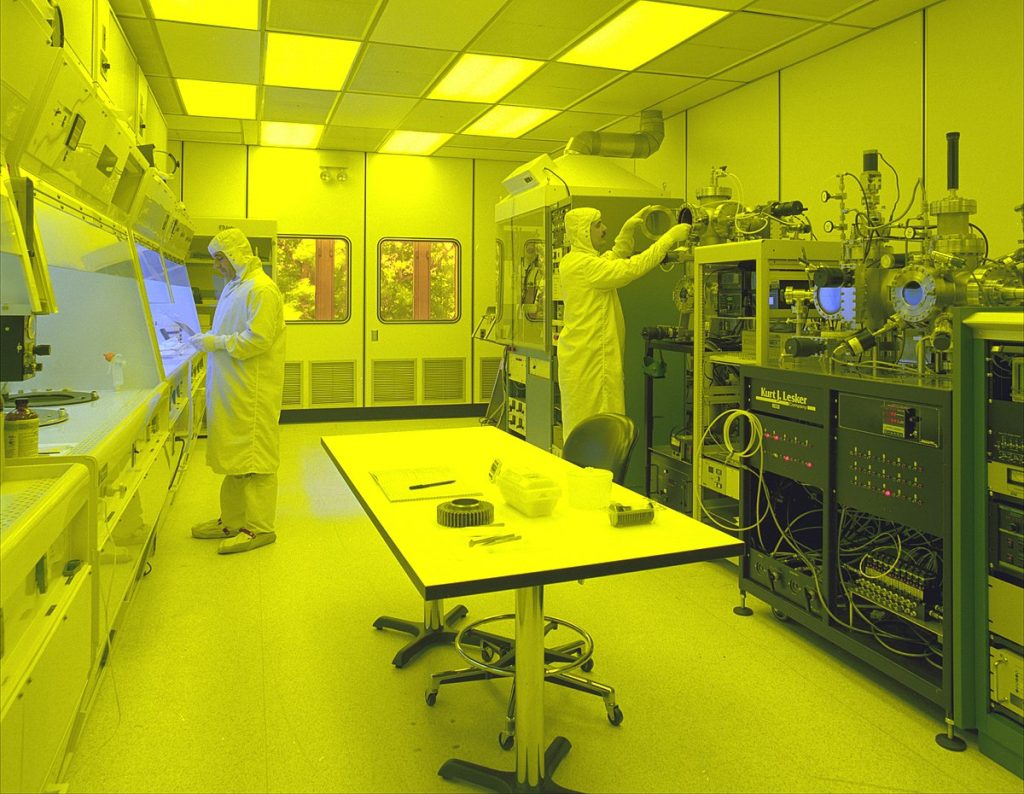
Una sala blanca o sala limpia (en inglés white room o clean room) es una sala diseñada especialmente para el control del ambiente en el que se fabrican productos electrónicos, dispositivos médicos, productos farmacéuticos y otros productos que requieren un ambiente controlado para su fabricación.
Estas salas están diseñadas para controlar la cantidad de partículas en el aire, la temperatura, la humedad y otros factores ambientales que pueden afectar la calidad del producto. Las salas blancas suelen utilizarse en la fabricación de productos que son extremadamente sensibles a las partículas en el aire, como los microchips, ya que esta suciedad podría depositarse durante los diferentes procesos de fabricación y terminar con chips defectuosos, lo que bajaría el yield o rendimiento, algo que dispararía los costes.
La sala blanca tiene una construcción especial para controlar la entrada de partículas externas y para mantener la circulación de aire. La sala está sellada para evitar la entrada de partículas y la entrada de aire se filtra para eliminar cualquier partícula presente. Además, las personas que trabajan en la sala blanca deben seguir procedimientos especiales de limpieza y vestimenta para reducir la cantidad de partículas que generan.
Para que estos ambientes se mantengan tan puros, también necesitarán de un equipamiento de control y monitorización de los diferentes parámetros que se necesitan mantener bajo control, como sensores para ESD, HR, temperatura, presencia de partículas, etc. Y estarán colocados a lo largo de la sala, para medir los parámetros en cada punto.
Dentro de una sala blanca para la fabricación de semiconductores se controlan varios parámetros ambientales para garantizar que el proceso de producción sea lo más limpio y controlado posible. Los parámetros más comunes que se controlan son los siguientes:
- Partículas en el aire: la cantidad de partículas en el aire se controla con filtros de aire de alta eficiencia (HEPA) que eliminan partículas de tamaño submicrométrico. El número máximo permitido de partículas por metro cúbico varía según el nivel de clasificación de la sala blanca, que se define en términos de ISO Clase (ISO 14644-1).
- Temperatura y humedad: la temperatura y la humedad relativa se mantienen en valores controlados para garantizar la estabilidad de los procesos de fabricación. La temperatura se controla mediante sistemas de climatización y la humedad mediante sistemas de humidificación y deshumidificación.
- Presión diferencial: la sala blanca debe tener una presión diferencial positiva en relación con las áreas circundantes para evitar la entrada de aire no filtrado. El flujo de aire se controla mediante sistemas de ventilación y se mide con medidores de flujo de aire. Por ejemplo, habrá algunas zonas con presión negativa para evitar que vapores químicos o partículas desprendidas en el proceso que allí se lleva a cabo contaminen otras zonas. Por otro lado, habrá zonas de presión positiva, para evitar la entrada de suciedad de otros ambientes. Por ejemplo, en la entrada de la sala limpia habrá una presión positiva, para que cuando se abra la puerta para que pasen los trabajadores, no se contamine el ambiente con el aire sucio del exterior. Además, también habrá salsas de descontaminación o limpieza donde se usan trajes especiales o bunny suites, y chorros para limpiar posibles partículas para que los trabajadores no entren suciedad.
- Contaminantes químicos: los contaminantes químicos se controlan mediante sistemas de ventilación y filtración que eliminan los gases y vapores tóxicos presentes en el aire. Los niveles de contaminantes químicos se miden con sensores de gas.
- Iluminación: la iluminación se controla para garantizar la visibilidad y el confort de los trabajadores. Las luces deben tener filtros para que no afecten a procesos de fotolitografía o revelado.
- Sensores ESD: para medir la presencia de electricidad electrostática que podría afectar también los chips que se fabrican.
- Otros: también puede haber otros sensores de fuego o humo para evitar incendios, etc.
Estos parámetros ambientales se monitorean continuamente mediante sistemas de control automatizado y se ajustan según sea necesario para garantizar que se mantenga un ambiente controlado y limpio dentro de la sala blanca.
Clases de sala blanca
Las salas blancas también se clasifican por el nivel de limpieza que pueden mantener. El nivel de limpieza se mide por el número de partículas en el aire de un tamaño determinado. Las salas blancas de menor clasificación permiten un mayor número de partículas en el aire, mientras que las de clasificación superior tienen un ambiente aún más limpio. Por ejemplo, tenemos el estándar ISO:
Clase | Máximo de partículas por m3 | Equivalente FED STD 209E | |||||
---|---|---|---|---|---|---|---|
≥0.1 μm | ≥0.2 μm | ≥0.3 μm | ≥0.5 μm | ≥1 μm | ≥5 μm | ||
ISO 1 | 10b | d | d | d | d | e | |
ISO 2 | 100 | 24b | 10b | d | d | e | |
ISO 3 | 1,000 | 237 | 102 | 35b | d | e | Class 1 |
ISO 4 | 10,000 | 2,370 | 1,020 | 352 | 83b | e | Class 10 |
ISO 5 | 100,000 | 23,700 | 10,200 | 3,520 | 832 | d,e,f | Class 100 |
ISO 6 | 1,000,000 | 237,000 | 102,000 | 35,200 | 8,320 | 293 | Class 1,000 |
ISO 7 | c | c | c | 352,000 | 83,200 | 2,930 | Class 10,000 |
ISO 8 | c | c | c | 3,520,000 | 832,000 | 29,300 | Class 100,000 |
ISO 9 | c | c | c | 35,200,000 | 8,320,000 | 293,000 | Room air |
Y también el estándar que se suele usar en EE.UU.:
Clase | Máximo de partículas por pie cúbico | ISO equivalente | ||||
---|---|---|---|---|---|---|
≥0.1 μm | ≥0.2 μm | ≥0.3 μm | ≥0.5 μm | ≥5 μm | ||
1 | 35 | 7.5 | 3 | 1 | 0.007 | ISO 3 |
10 | 350 | 75 | 30 | 10 | 0.07 | ISO 4 |
100 | 3,500 | 750 | 300 | 100 | 0.7 | ISO 5 |
1,000 | 35,000 | 7,500 | 3000 | 1,000 | 7 | ISO 6 |
10,000 | 350,000 | 75,000 | 30,000 | 10,000 | 70 | ISO 7 |
100,000 | 3.5×106 | 750,000 | 300,000 | 100,000 | 830 | ISO 8 |
En la actualidad, no solo existen salas de Clase I, existen incluso salas de hasta 10 o 100 veces más limpias que eso para las foundries más avanzadas. Y, para que te hagas una idea, estas salas son miles de veces más limpias que cualquier quirófano. En una vivienda media, se pueden tener hasta 500.000 partículas por metro cúbico de aire… ¡Demasiado sucio!
Maquinaria y herramientas usadas
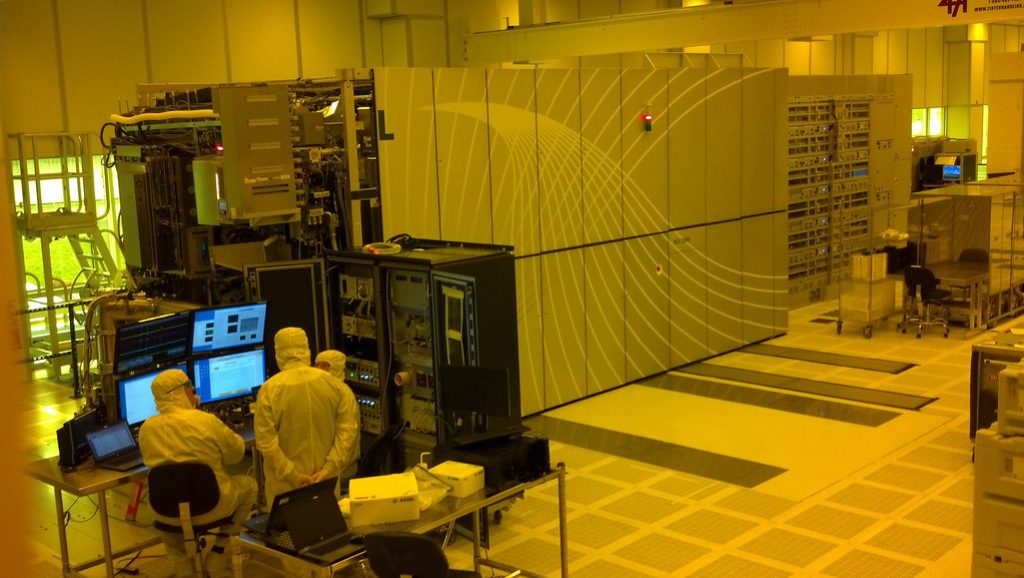
La fabricación de chips es un proceso complejo que requiere de una variedad de maquinarias y herramientas especializadas. A continuación, se presenta una lista no exhaustiva de algunas de las maquinarias y herramientas utilizadas en la fabricación de chips:
- Equipos de limpieza: se utilizan para limpiar las obleas de silicio y otros materiales antes de su procesamiento. Ejemplos incluyen equipos de limpieza por plasma y por inmersión en químicos.
- Equipos de litografía: se utilizan para imprimir patrones de circuitos en las obleas. Ejemplos incluyen impresoras de máscaras, sistemas de exposición de rayos ultravioleta (UV) y sistemas de proyección de haz de electrones (EB). Son los equipos más caros, y pueden costar cientos de millones de euros.
- Equipos de deposición: se utilizan para depositar capas de material en las obleas. Ejemplos incluyen equipos de deposición de vapor químico (CVD), deposición de capa atómica (ALD), deposición de sputtering y deposición de electrochapado.
- Equipos de grabado: se utilizan para grabar patrones de circuitos en las obleas. Ejemplos incluyen equipos de grabado por plasma y grabado químico.
- Equipos de medición: se utilizan para medir la calidad y las características de las obleas y los chips. Ejemplos incluyen microscopios electrónicos de barrido (SEM), espectrómetros de masas y sistemas de pruebas eléctricas.
- Equipos de unión y montaje: se utilizan para ensamblar los chips en paquetes y encapsulados. Ejemplos incluyen máquinas de unión por soldadura, sistemas de encapsulado por inyección y sistemas de envasado al vacío.
- Equipos de pruebas: se utilizan para probar la funcionalidad y el rendimiento de los chips. Ejemplos incluyen sistemas de prueba de circuitos integrados (IC) y sistemas de pruebas eléctricas automatizadas.
Además de las maquinarias y herramientas mencionadas, la fabricación de chips también requiere de suministros y consumibles como obleas de silicio, gases de proceso, químicos y agua ultra pura.
Y, para finalizar, te dejo este vídeo en el que comprenderás mejor todo lo visto anteriormente, y verás cómo son realmente estas fab por dentro: